Brief:
Mostly seen at air shows and museums today, many rocket ship fans can still remember when the tri-engine Irhydavi played a significant role in history. Before the catastrophic defeat of the India-Paskistani Free States by China in the second Asian War (February 20-22, 2366), the Irhydavi was the premier fighter-rocket of the IPFS. It proved no match for the superior weaponry of the Lao Hu fighter. The surviving ships ferried hundreds of imminent IPFS scientists, artists, and their families to safety in the waning hours of the war. These included 3-year old Sara Pranjal, now president of the United States of North America.
The Irhydavi is futuristic 3 x 18mm cluster kit bash of the Semroc Hydra VII, created for the 2006 EMRR Challenge. The original Semroc kit is a nifty 7 x 18mm cluster design built from a large variety of high quality parts. Based on the kit's parts and instructions, I think Semroc's kit looks like a great deal at only $23.
Modifications:
Circumscribe the ring fin with two lines, 0.25" from each end. Between these margins, inscribe 3 up-down zigzags. Cut along zigzags and glue flat edges together, forming the shape shown in the photos.
- Assemble the three main fins from the balsa parts as shown in the photos. Three of the original strake fins will also be used for the Irhydavi, however, I trimmed the fat end of each strake for a more pleasing angle. Three strake extenders can be formed from spare balsa in the kit. In the finished photo, the main fins are blue and the strakes (below the ring) and strake extenders (above the ring) are red. Sand (and fill in gaps with Elmer's Fill 'n' Finish), bevel, and seal fins. Sand and seal all nose cones. Fill and sand spirals on all tubes.
- Cut three BT-20 tubes to 7" and glue an engine block in one end of each at a distance suitable for standard 18mm motors. Tie the shock cord through one of the tube walls on the end opposite the engine block. Insert these three tubes in cluster formation 2.5" inside a BT-60 tube, leaving 4.5" extending. It is a very snug fit. Fillet tube seams and fill the gaps where the cluster of tubes enters the BT-60 using spare materials from the kit. For strict kit bash, motor retention is by friction fitting. Otherwise I'd recommend gluing a bolt between the three motor tubes with a nut and single washer to retain the three motors.
Draw 6 equal spaced guide lines along the length of the BT-60 assembly with three lines where the BT-20s touch the BT-60 wall and three lines aligned with the seams between the BT-20s. Extend the first three lines along the BT-20 tubes.
- Glue main fins along BT-20 guide lines. Pull on the ring assembly with alignment as shown in the photos. Glue. Next glue the strakes on aligned with the seams between BT-20s. Finally, glue the strake extenders. See photos for partially- and fully-completed tail assemblies.
- Cut three 2" portions of BT-20. Cap one end of each with thrust rings and cardboard caps from kit. Glue nose cones on other ends. Glue one of these weapon pods to each main fin as seen in the photo.
To form the upper part of the rocket, the BT-60 nose cone is used as a transition, with a BT-20 tube forming the uppermost portion of the rocket. The easiest way to get perfect alignment is to create a jig using the unused BT-60 tube and two spare 20-60 centering rings. (If you don't want to make a jig, just eyeball it.) To try the jig, dry fit a BT-20 into the BT-60 using the centering rings. Slide the whole assembly down so the BT-60 nestles on the pointy end of the large nose cone. Now that you understand how it should work, do it again with glue to attach the BT-20 to the nose cone. Do not let glue get on the BT-60 tube or the CRs. When the glue is dry, pull of the BT-60 jig and the centering rings. See the photo illustrating the jig assembly (top) and usage (bottom). Fillet the joint between the BT-20 tube and the BT-60 nose cone and drop more glue inside the BT-20 to ensure a bombproof attachment.
- Cut enough additional BT-20 to make a total length of 11" above the BT-60 nose. To form a coupler, take another small segment of BT-20 and cut out a thin strip lengthwise. The width of the strip should be a couple millimeters. Bring the edges back together and snuggle this as a coupler inside the BT-20s you are joining together.
Using much of the remaining balsa, glue layers together to form a balsa block to make the nose cone. Drill a hole in the fat end and glue in one of the dowels from the kit. Put this in your electric drill to use as a crude lathe. Use sandpaper to "turn" a suitable BT-20 nose cone. See the photo for the before and after. This is a tough skill to master, so simply use a spare BT-20 nose from your parts drawer if you're not trying to adhere strictly to kit bash limitations!
- Insert 2oz of nose weight into the uppermost BT-20 just below the nose cone. Swing test the fully assembled rocket to ensure stability. Glue or fasten the nose cone in place.
- Glue the bulkhead to the unused BT-60. Insert the hook into the bulkhead. Glue or fasten the BT-60 nose cone, which now forms the base of the upper rocket portion, into the other end of this tube. Construct the stock parachute kits and attach them as in instructions: two to the Kevlartied to the aft body and one to a short piece of Kevlar® tied to the Kevlar® onto the bulkhead hook in the forward body. (Alternatively, use larger chutes for slower descent.)
- Bisect and bevel the launch lug, then suitably attach the two lugs to the body. Finish your rocket with paint and use the kit decals if desired. Painting is tricky because many of the fins extend between the ring and body. With careful masking and repeated light spraying, a pretty finish is possible. One could also consider pre-painting some parts or applying by brush on the final assembly.
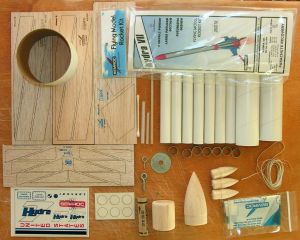
Construction:
A "kit bash" means to invent a new rocket using only the parts in the original kit. Nothing may be added (except nose weight). The Irhydavi adheres strictly to this limitation--even in its name--however, I also note several instances where construction could be greatly eased with a few spare parts. This kit bash uses most of the Hydra VII parts with a few balsa strips, BT-20 tubes, and odds and ends left over for other projects.
The Irhydavi is 38" tall with a total weight of 7.875oz. With three C6-5 motors, it sims to around 850 feet. Construction under strict kit bash limitations was pretty tricky including assembling the large fins from many odd balsa parts and turning a handcrafted nose cone. If you allow yourself a spare sheet of balsa and an extra nose cone, it would be quite a bit easier.
Flight:
Prepped with 3 x C6-5 motors, we set off to launch. The first launch was stable and straight with moderate height of maybe 700ft. Ejection was a hair early, and all the laundry came out fine. Top and bottom halves recovered separately, gently, and with no damage. On the second flight, only 2 of the 3 C6-5 motors lit, yielding a shorter flight to maybe 500ft with late ejection. Again, recovery was trouble free. The third flight was the best, at least on the way up. All 3 C6-5s lit and the rocket shot up to its full expected altitude of about 850ft. Ejection was exactly at apogee with the rocket horizontal. The aft section recovered perfectly, but something went wrong with the nose chute. It appeared that the nose section came in ballistic with no chute attached. I thought the Kevlar had snapped because we saw no flapping or dangling stuff. The nose section coresampled the full length of the nose cone. This failure was mystifying because at the impact site, the nose chute was fully deployed, untangled, unmelted, attached, and looked like an absolutely normal recovery. Some strange sort of entanglement must have occurred. The nose portion of the rocket is easily repaired or replaced, so Irhydavi will certainly fly again.
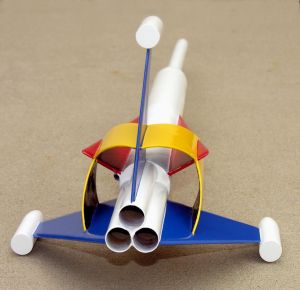
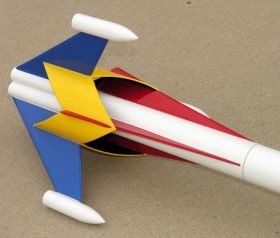